In today’s marketplace, where regulatory requirements are increasingly more stringent and consumer satisfaction is paramount, establishing a high-level quality management system should be a priority for businesses of all sizes. Whether in manufacturing, foodservice or healthcare, an effective quality system not only provides a competitive advantage by guiding the organization toward improved performance but more importantly, it is a key factor in mitigating product and business risk by detecting and preventing defects along the way. The quality system maintains a state of control for the business and personnel, defines processes, policies and standards, and contributes toward a predictable product quality outcome. But determining when, how and at what cost—taking into consideration both financial and human resources—to implement quality processes in a new enterprise where none have existed before can be an overwhelming task for startup entrepreneurs.
When launching a new business, mapping out quality processes up front is as important as establishing a well-thought-out business plan. It’s not surprising then that a quality system should be integrated into the business plan, and at the beginning of the product development process. Furthermore, involving the entire development team at the onset creates a culture of continuous improvement and ensures regulatory requirements are established, understood, and executed successfully. Failure to adopt a quality system early in the development process could result in significant financial costs if the product does not perform as intended in the field.
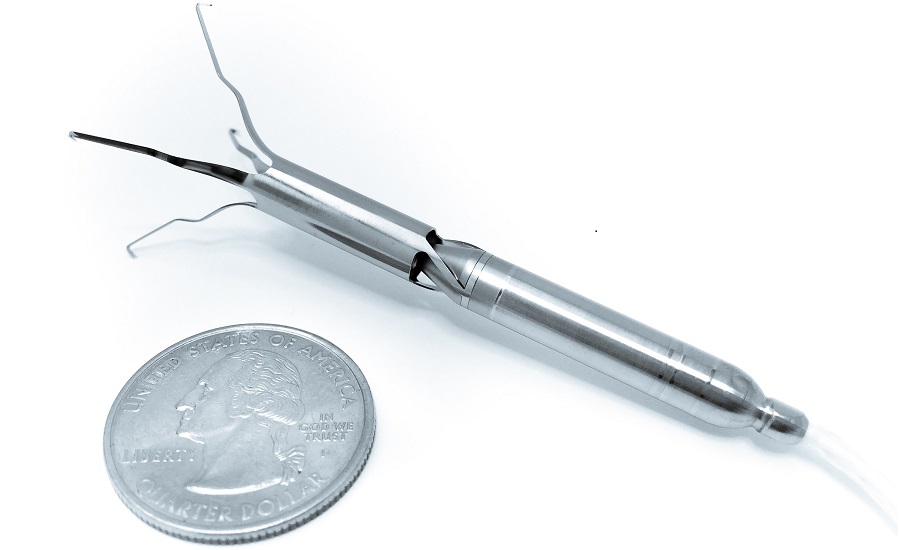
The quality system is not a static manual of compliance content. Implemented within a dynamic business and regulatory environment, the quality system should respond, adapt and evolve throughout the development lifecycle. Working in tandem, the business plan and quality system provide a roadmap for successfully reaching milestones: identifying the regulatory environment; customer and product requirements and risks; and the rollout of final product. Moreover, understanding the organization’s strategy to market and having a clear vision of business needs will help determine which are the most appropriate quality processes and procedures to implement and the appropriate timing for implementation.
For early-stage startups with limited resources, building in the essential quality components as they are needed is most cost effective and efficient. At a minimum, the four elements of a quality system that should be put in place at the development planning phase are risk management, design controls, document controls and personnel training. As the product evolves into detailed engineering design and process development planning, other elements are added such as supplier controls, process and production controls, equipment controls, purchasing controls and corrective and preventive action. Finally, when transitioning into pilot production for design qualification and product commercialization, customer-related processes including distribution, installation, servicing and complaint handling should be implemented into the quality system.
Startup CEOs should be wary of “one-size-fits-all” quality software systems, which can be financially disastrous and a time waste for a budding enterprise. Typically, these off-the-shelf programs include a litany of non-applicable document sets and directives for organizational departments that may not yet exist. Because they don’t accurately take into consideration an organization’s business strategy, these complicated quality systems more often create a product and business development bottleneck. Additionally, many comprehensive electronic quality systems in the marketplace charge maintenance fees as high as $50,000 annually. For small businesses with limited funds and time-strapped managers, or managers that lack the bandwidth to fully understand and implement quality software systems, outsourcing is a strategic choice.
Securing the services of a quality assurance specialist, as either an external consultant or a full-time resource, to provide an objective audit of the current situation, identify problems and offer potential solutions is an efficient and effective solution for startups. While many quality assurance professionals carry auditor training and QA manager certifications, look for those with hands-on experience in a new enterprise, especially consultants that have transitioned to commercial or successful acquisition. Another added benefit to aligning with an expert that has worked exclusively within quality systems means they have likely learned from the regulatory pitfalls that other companies have faced and are able to overcome these problems. An experienced consultant will begin the process by understanding the company’s needs and product requirements and will then explain deliverables, provide training, and establish continuous improvement procedures and an actionable timeline. An expert will develop an effective quality system based on what is best for the organization, thus realizing benefits early and providing quick returns on investment.
Improving quality shouldn’t impede product development or bury executives in mountains of confusing paperwork. An agile quality management system that evolves with the ever-changing business and regulatory environment will decrease time-to-market, reduce risk and ensure customer and compliance needs are met in a cost-efficient manner. While the pursuit of quality can be a costly line item, successfully establishing accurate product requirements and risk mitigation strategies early on will result in significant savings over the product development lifecycle.